DIYを続けていると「作業台」が必要になりませんか?
もし「作業台は必要!」っと思った方はすでにDIYで何か作り上げてる人でしょう。
今回はDIY初心者でも作りやすい「ソーホース」作りにチャレンジします。
- 「ソーホース」の良いところ
- コンパクトに折りたためる
- 収納しやすい
- 2×4材だけで簡単組立
- 好きな高さにできる

収納しやすい作業台を目指しました!
簡単に済ませたい方へ
これから解説をはじめますが、「丸ノコやサンダーを購入」「木材を斜めに切断」など少し手間のかかることが出てきます。
「簡単って言ったのにめんどくさそー」っと思った方はそんなの無視して大丈夫です。
少し僕なりのこだわりを入れたら面倒になってしまいました。
切断はホームセンターでできます。
斜めカット無しでもちゃんと立ちます。
雨や耐久性を気にしなければ塗装しなくても大丈夫。
木材は磨かなくても塗装はできます。
DIYなので自分のやりたいようにやればそれでいいのです!
天板受け木材の固定方法なんて強引に加工してます。「これで良いかも」と思ったことをしてみただけです。

参考になる情報があれば嬉しいです。
それでは解説を始めます!
必要な工具と材料
丸ノコとサンダーを購入
ハイコーキ製丸ノコを買いました⬇︎
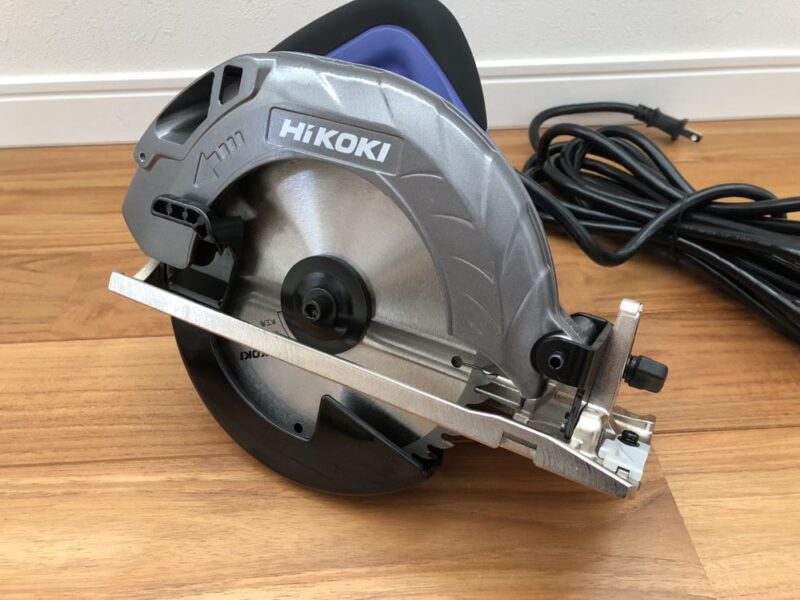
- 特徴
- アルミベース
- 刃直径165mm
- 価格1万円以下
値段も1万円以下、評価◎で初心者には十分です。
だけど、キックバックが少し怖くて購入を迷ってました。

キックバックは本当に危険ですので勉強しました。取り扱い注意です!!
ボッシュ製オービタルサンダーを購入⬇︎
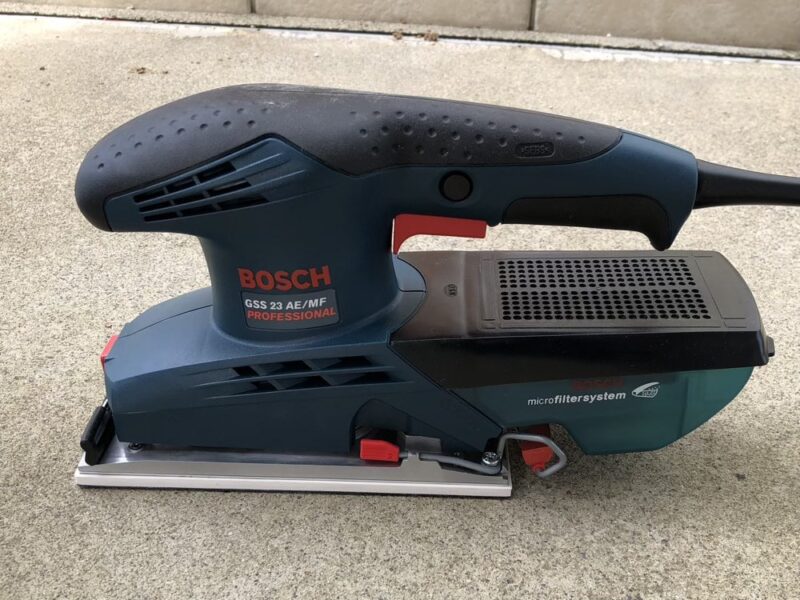
塗装前の木材磨きに大活躍してくれました!
やはりですが、工具でやるのと人力では全然進むスピードが違います。
材料はソーホースと2×4材だけ
ソーホース2個入り×2セット⬇︎
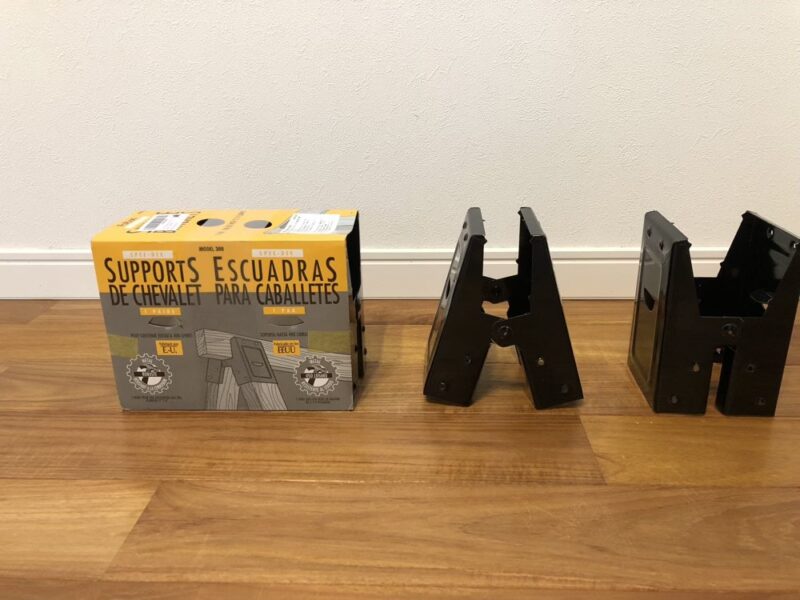
- 特徴
- 型番400と300がある
- 耐荷重が高いのは300
耐荷重は300タイプで1台(1セット)約180kgみたいです。
400タイプは約135kgみたいです。

僕は耐荷重が高い300タイプを購入してます。
2×4材6フィートを5本購入⬇︎
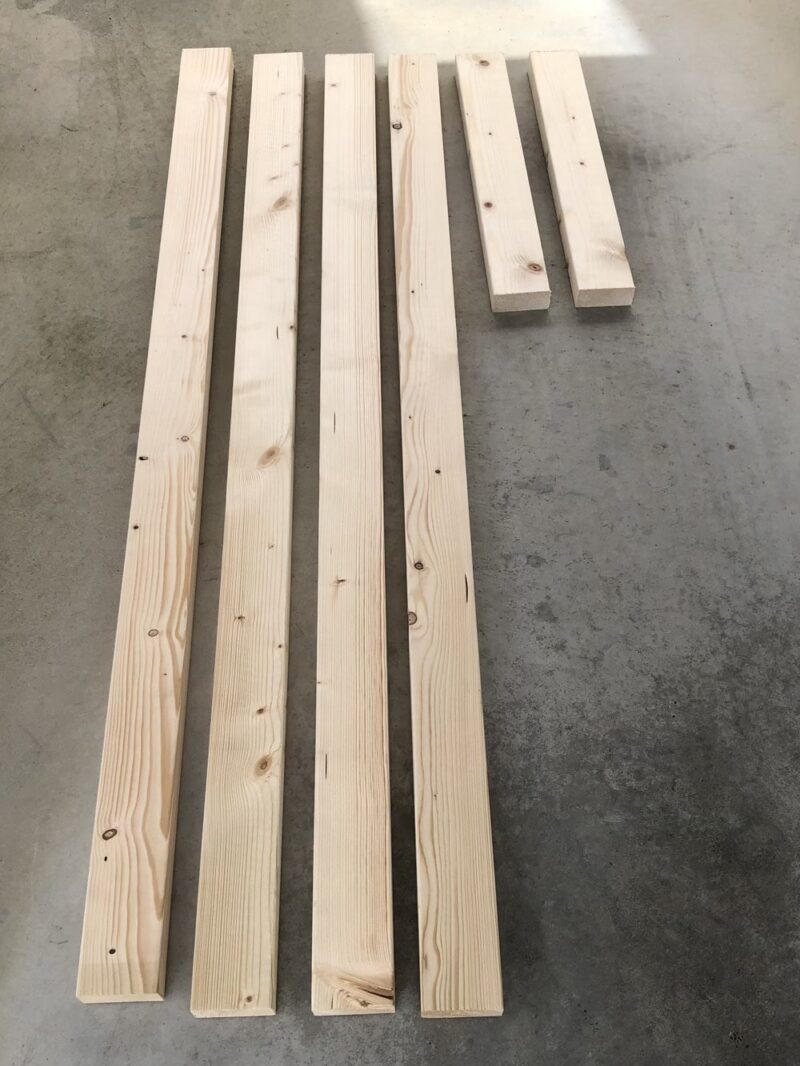
ホームセンターで必要な長さにカットしてもらいました。
- 足の材 1671mm × 4本
- 天板受け 600mm × 2本
足の材は斜めカットして2本になります。(後ほど詳しく解説!)
作業台高さを決める計算
作業台の高さ決めに下記の公式があります。
(身長÷2)+靴底高さ5mm
ネットで探すと人間工学からきてるようです。しかし、公式の違いがあり、本当かわかりませんがこれを一つの目安にしました。
悩んだ末に906mmの高さに決めました。天板の厚み分24mmを載せるとちょうど930mmの高さになります。
足の材は斜め13度にカット
ソーホースを開いたときに「足元を13度」にカットすると地面と平行になります。
そして、斜めカットした時に足の材が2本(同じサイズに)できるように設計図を書きました⬇︎
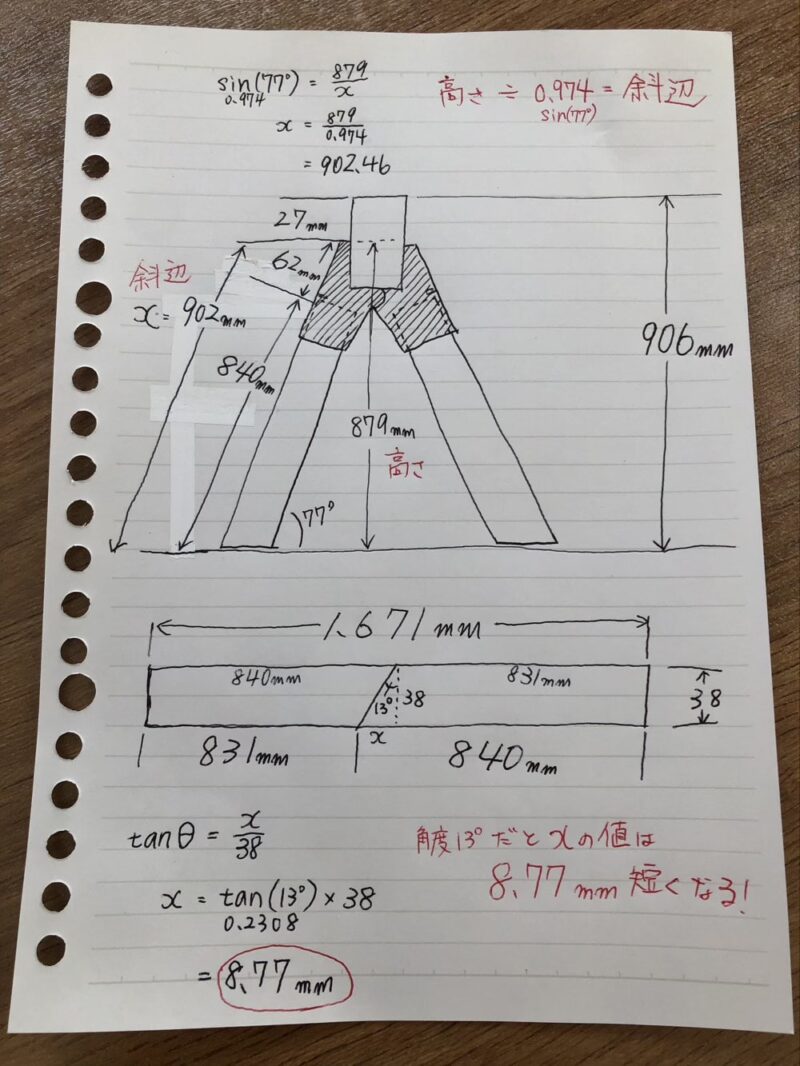
ちょっと見ずらいですが、1671mmの木材を840mmの位置から13度の角度で切断すると2本同じ長さの足ができる計算です。
僕も混乱するのですが、ポイントを抑えると木材の長さが計算できます。

これで木材を無駄なく使えます。
※すいません、この図面だと丸ノコの刃幅分を含めていなかった為に数ミリのズレがでました。(後ほど写真あり)
足の長辺の求め方
(求めるソーホース台の高さ)-(天板受け突出量27mm)=高さ
高さ÷0.974=斜辺
斜辺-(ソーホースストッパー位置62mm)=足の長辺の長さ
ホームセンターでカットしてもらう長さ
(足の長辺の長さ)-8.77mm=足の短辺の長さ
(足の長辺の長さ)+(足の短辺の長さ)+丸ノコ刃幅分約2mm=ホームセンターでカットしてもらう長さ
木材を斜めにカット
丸ノコの角度を13度に設定します。
レバーを緩めて、目盛りを13辺りに移動⬇︎
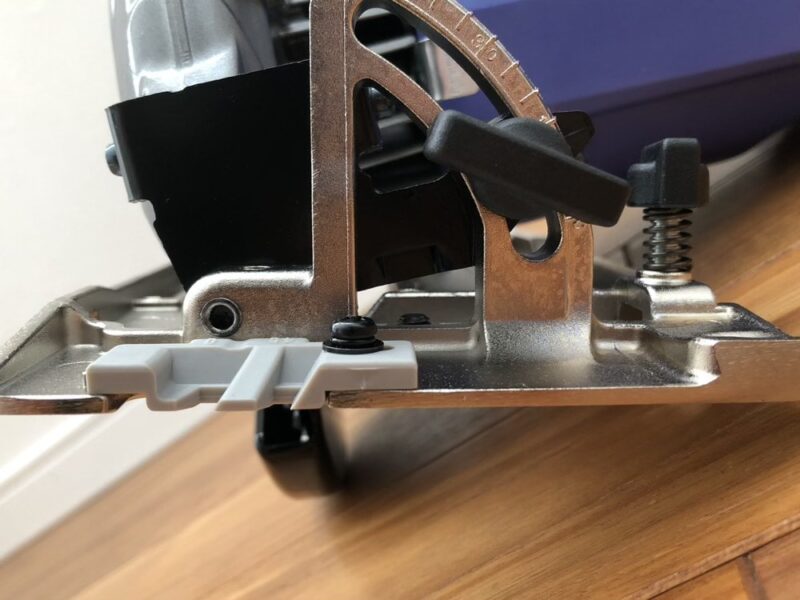
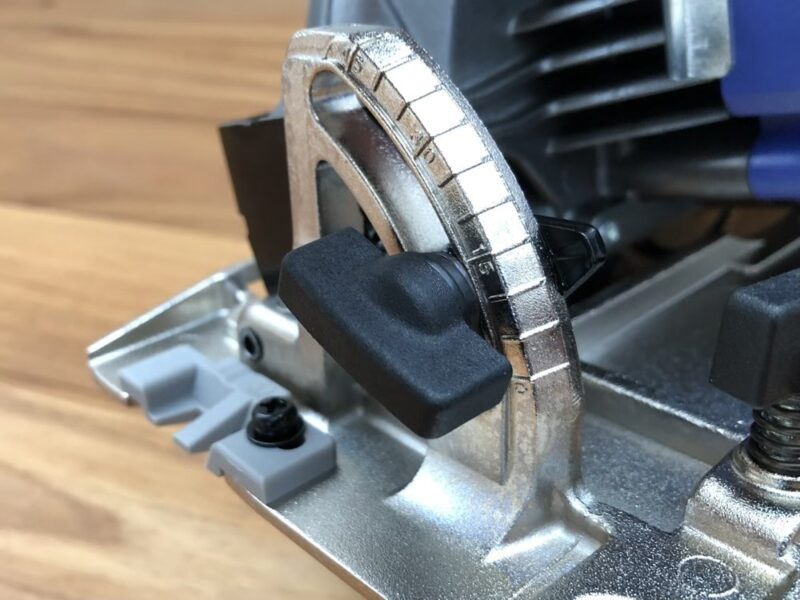
分度器も無かったので大体で決めました。
木材は840mmのところに印をつける⬇︎
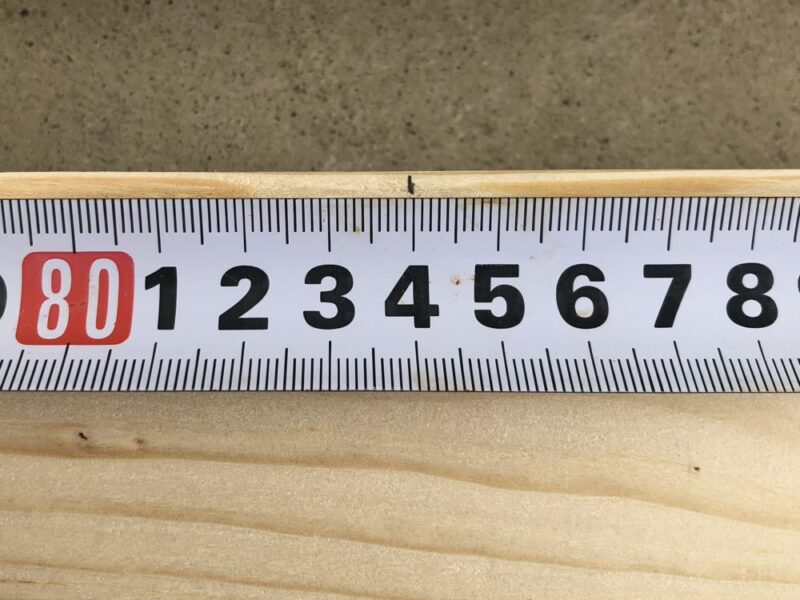
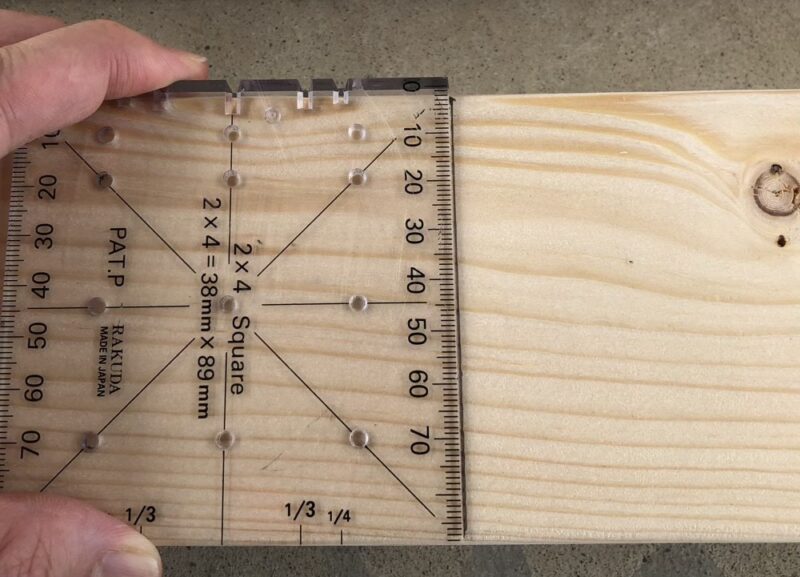
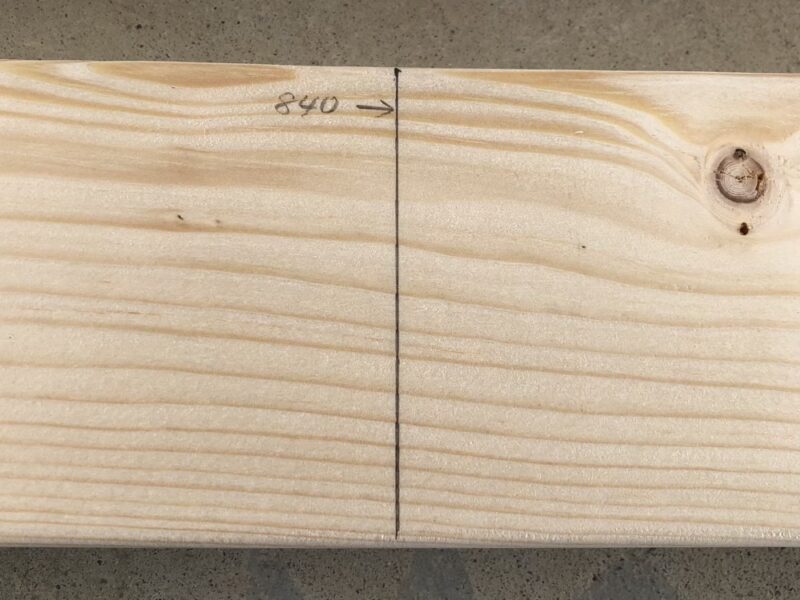
他の材料で作業台代わりに。
真っ直ぐカットができる丸ノコガイドを用意して。

そして、丸ノコでゆっくりカットしていくと。
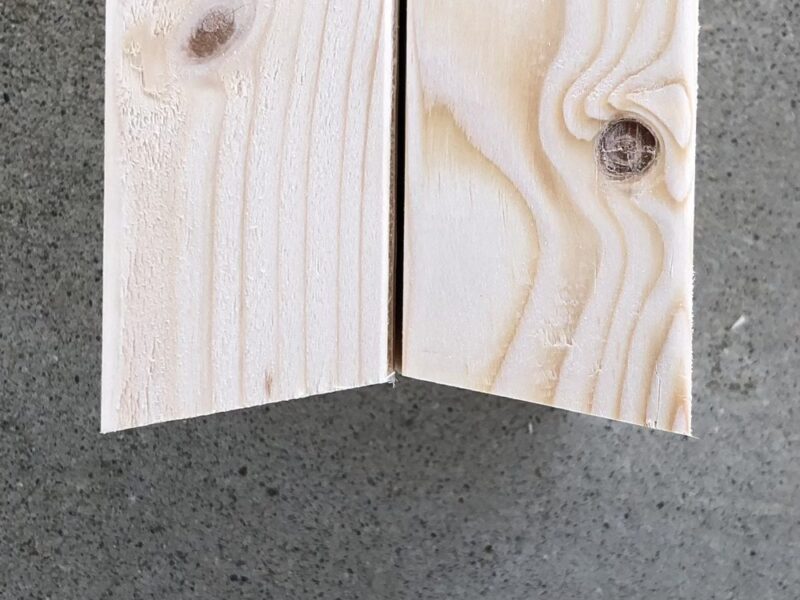

緊張しましたが、無事に切れました!

しかし、並べてみると長さに数ミリのバラツキがあります⬇︎

丸ノコ刃幅分が減少することを考えていませんでした。切断する際は刃幅分も考えないといけないですね。
仮でソーホースに取り付けてみます。
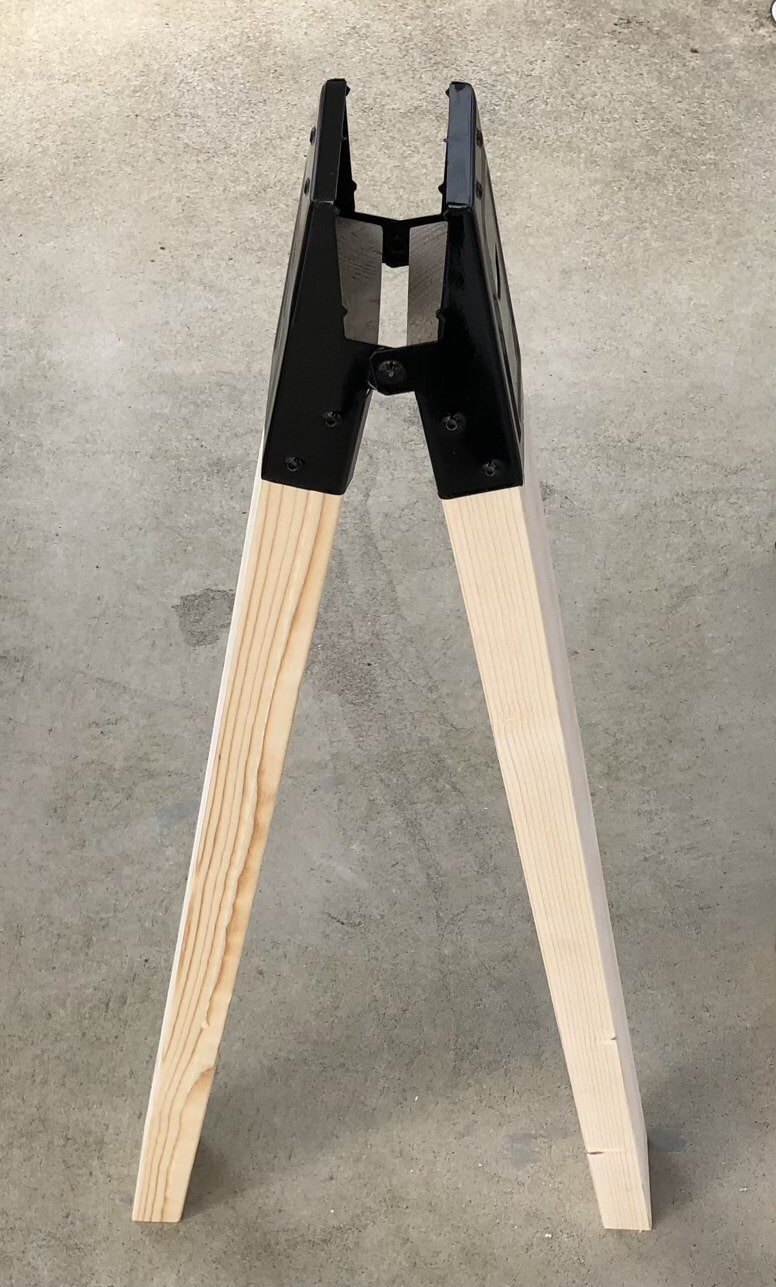
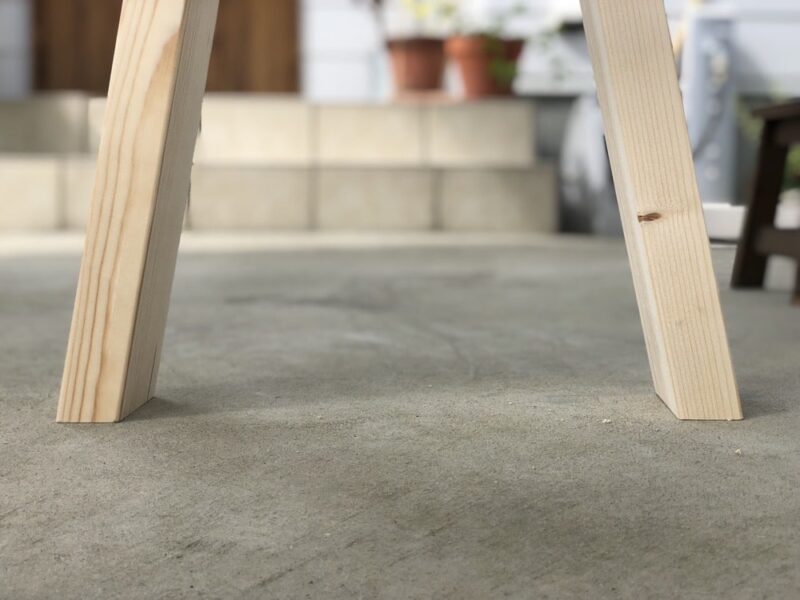

足元の角度も地面と平行になりました。
塗装
サンダーで木材を磨いていきます!
付属で入っていたペーパーを取り付けました。
ボッシュ製オービタルサンダーは専用ペーパーならマジックテープで簡単にくっつきます。もちろん市販のペーパーも切って挟むことができます。
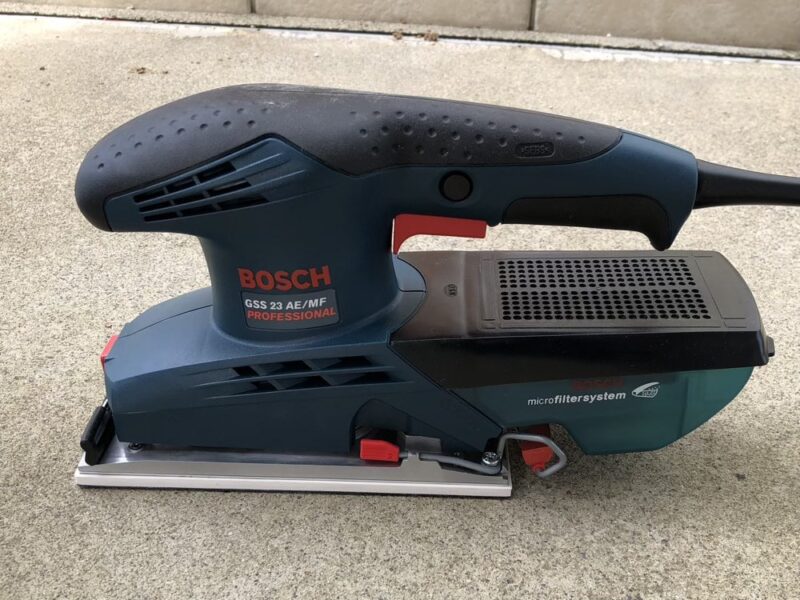
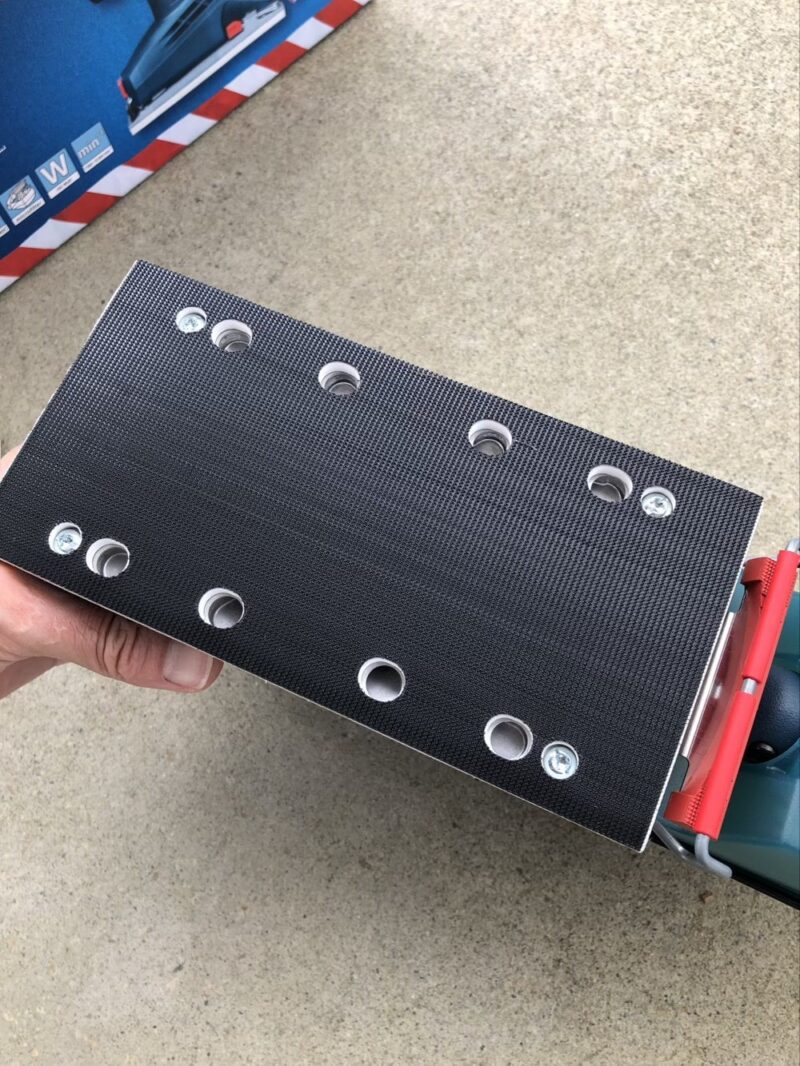
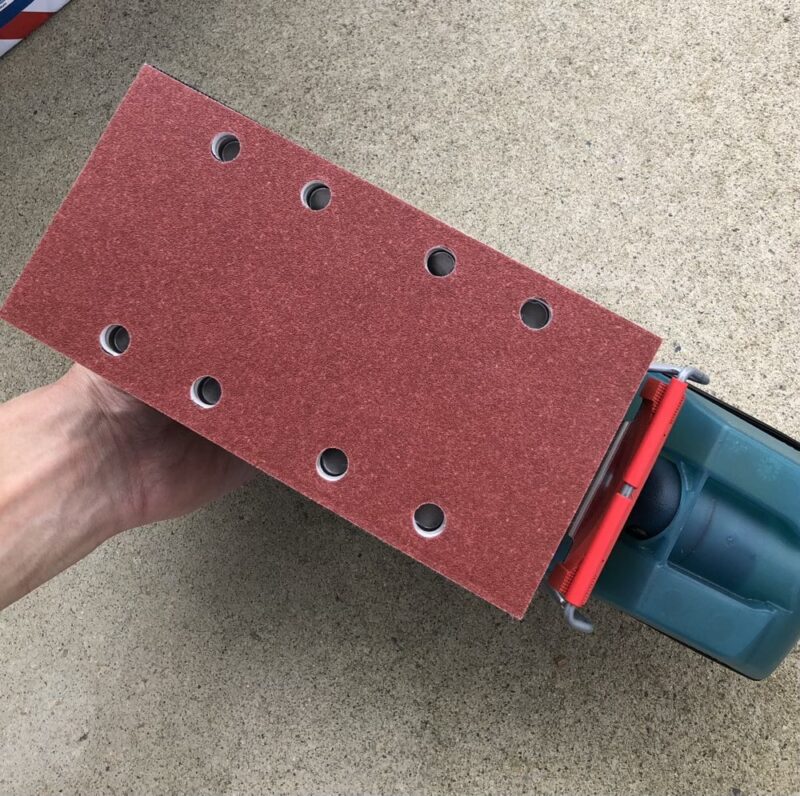

電動工具は格段に作業スピードを上げてくれます!楽です。
磨いたら塗装します⬇︎
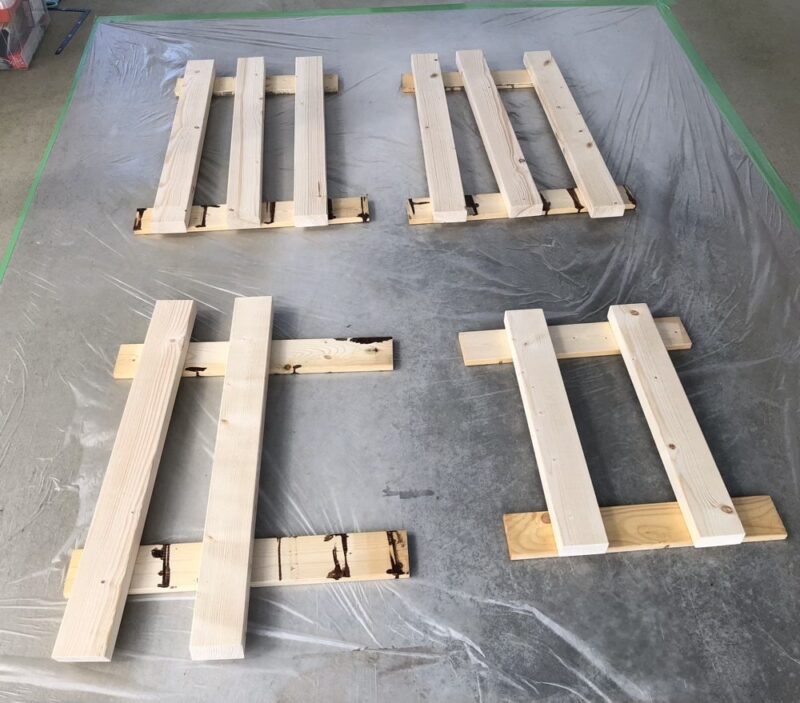
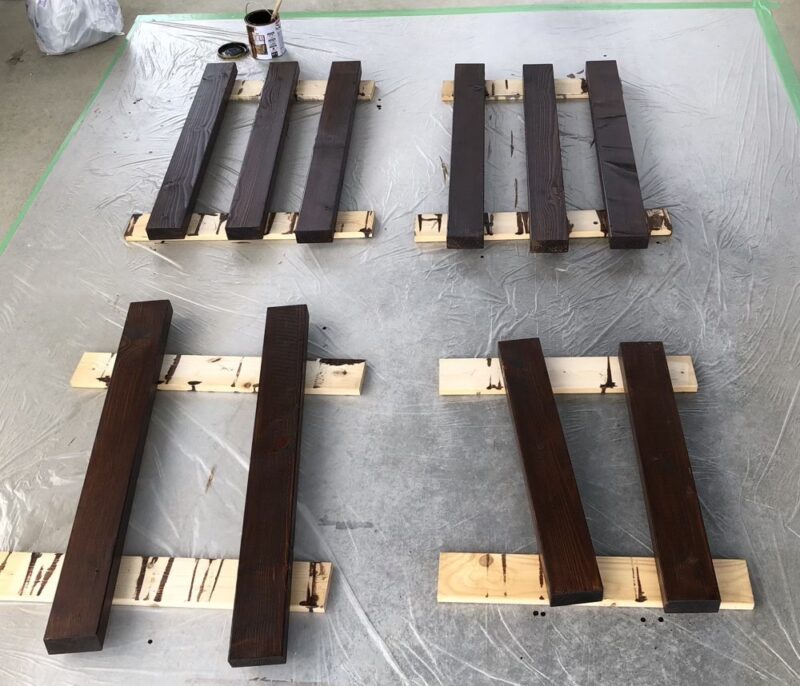
色はウォルナットで、2度塗りしました。
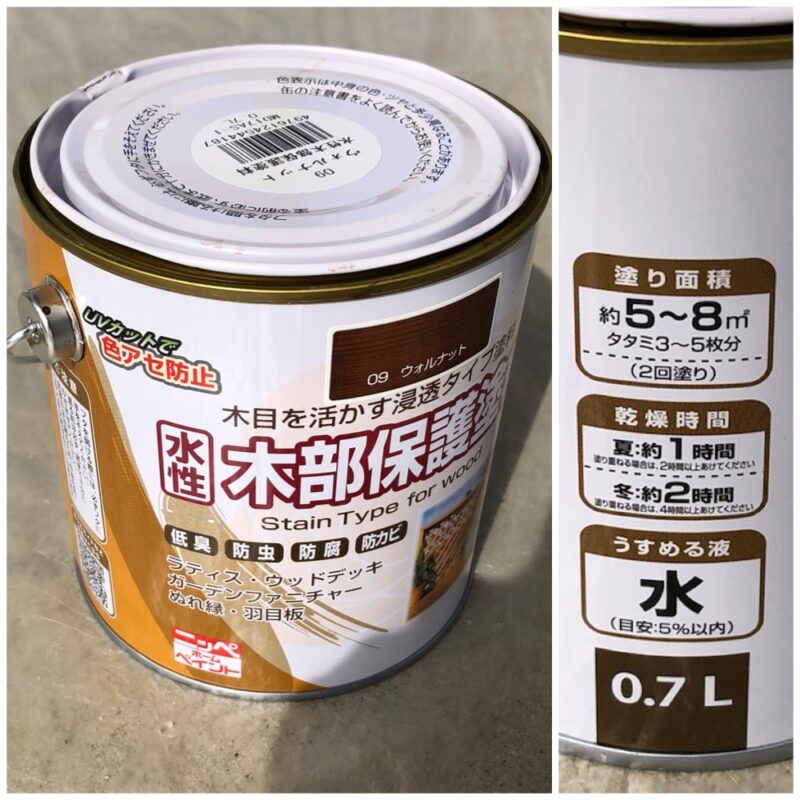
電動工具のおかげで切断から塗装まで半日で終わりました!
1日目は終了です。
ブラケットに木材を組み立てる
2日目は木材とソーホースを組み立てます。
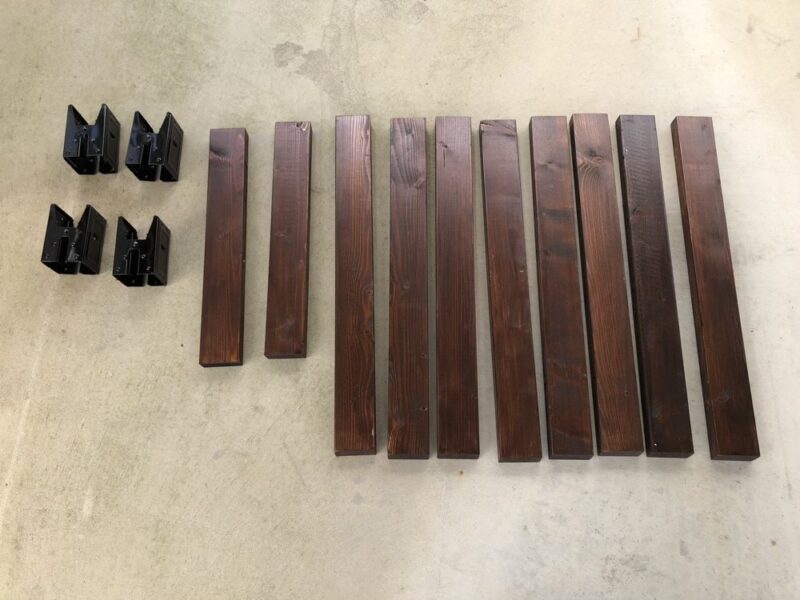
ソーホースに入れにくい
ソーホースに木材を入れてみたのですが結構キツイです。
無理矢理いれて木材が削れてます⬇︎
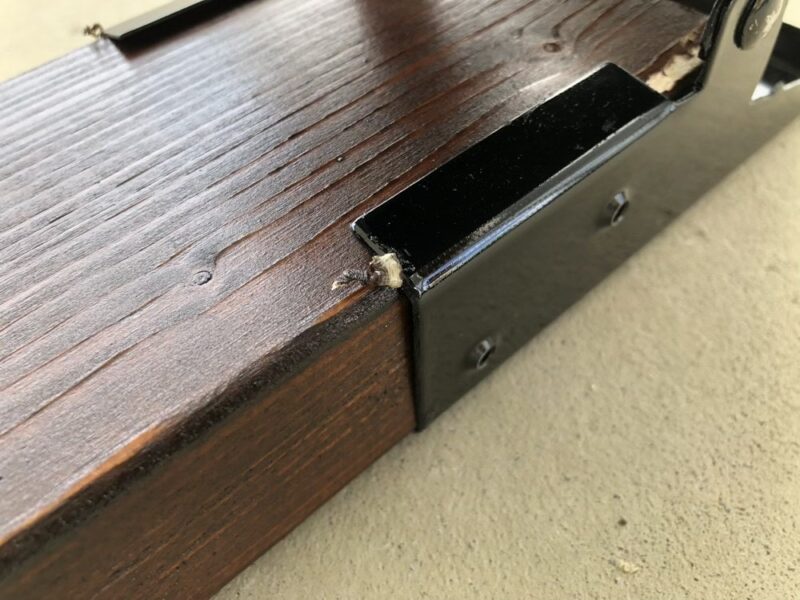
対策として、プライヤーで少し広げました⬇︎
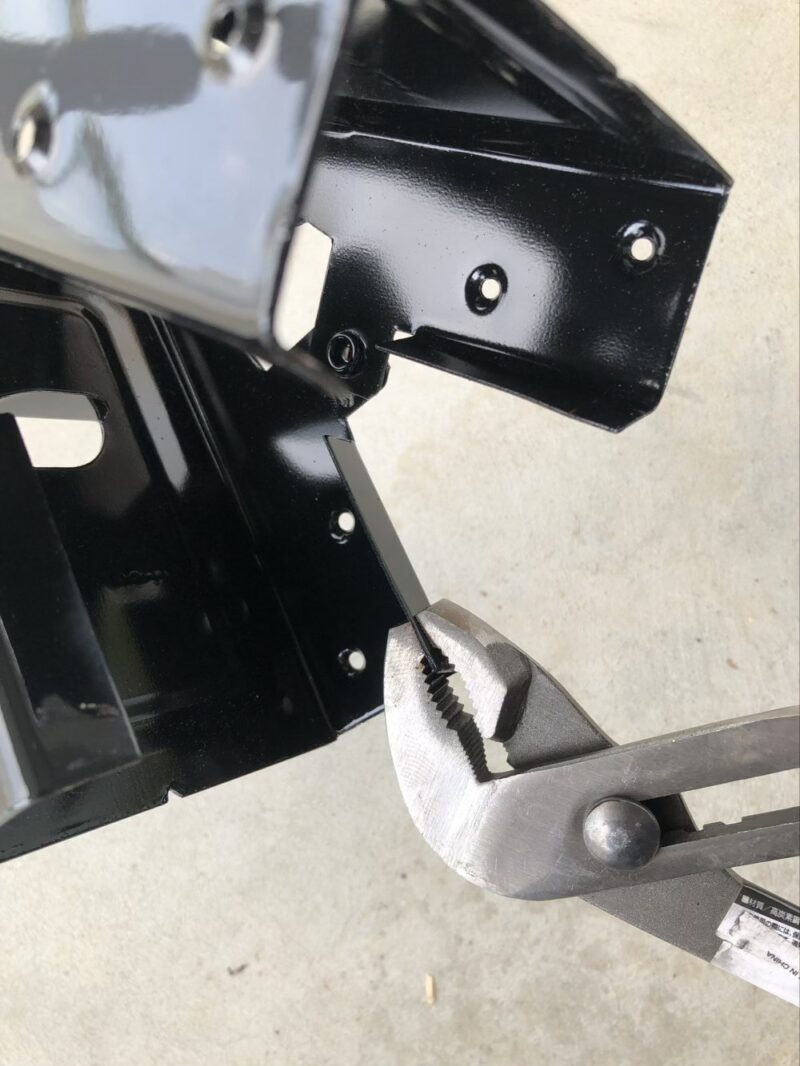
ソーホースと木材をネジで接合
キチンと奥のストッパーまで木材を入れます⬇︎
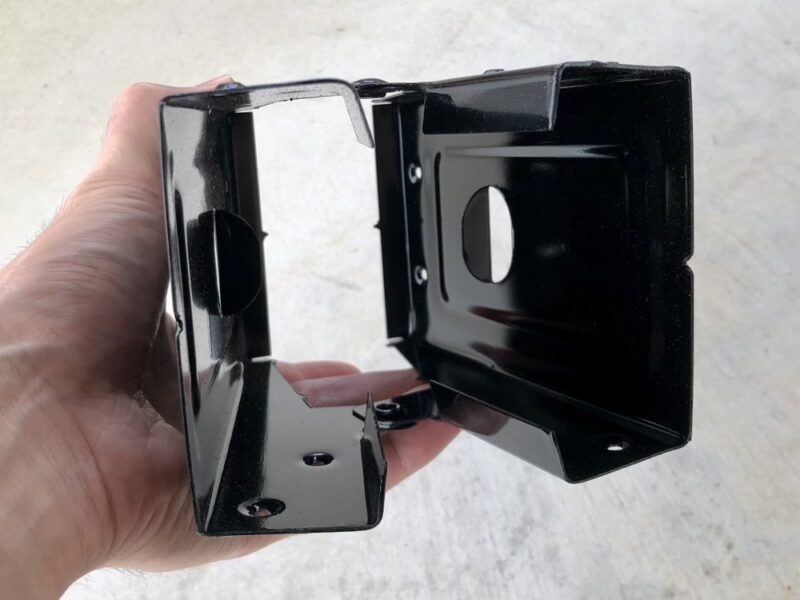
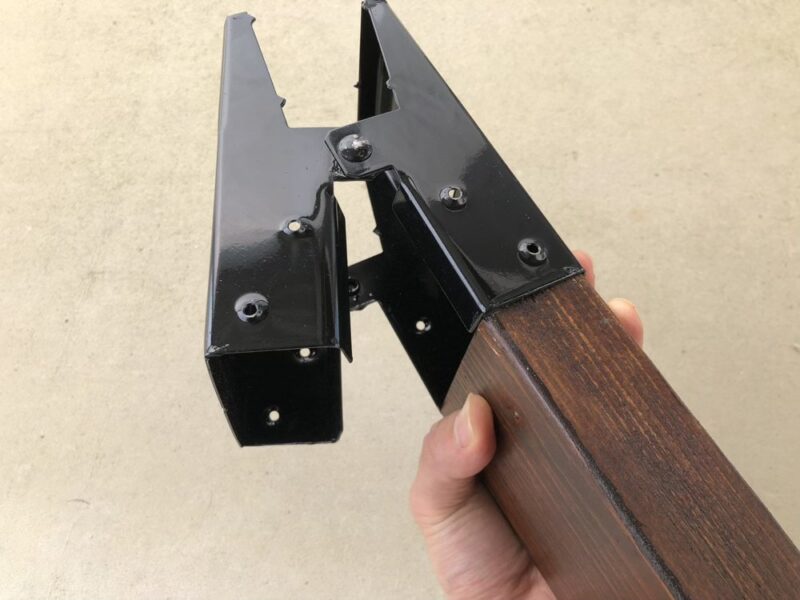
奥まで入ったのを確認し、ネジで接合。
余っていたタッピングネジを使いました。金属用ですが木材にも使用OKです⬇︎
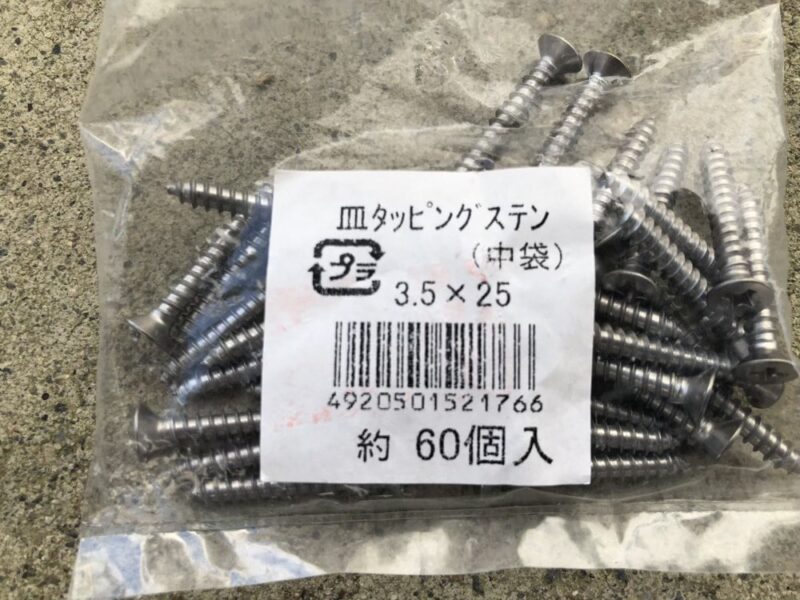
いつも下穴を開けてからネジを打つのですが、今回は直接インパクトドライバーで留めました⬇︎
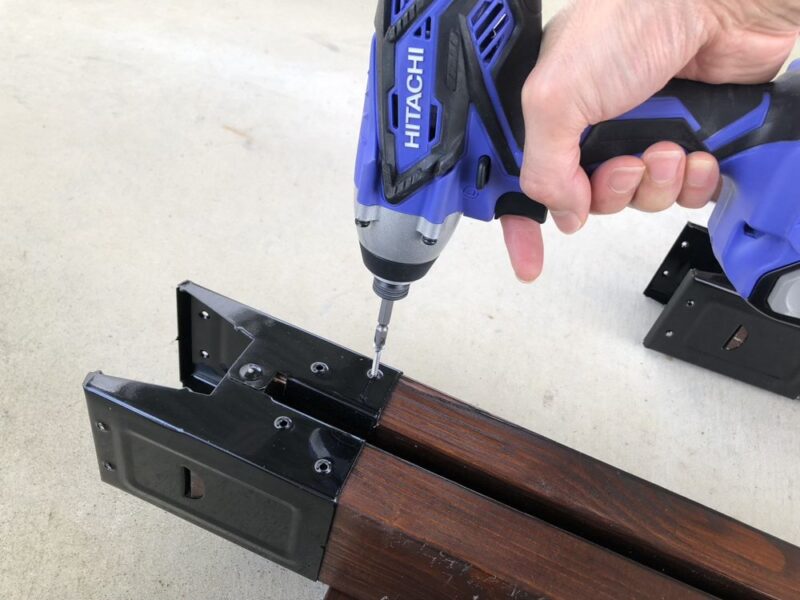
抑えが甘く、ネジからインパクトドライバーが外れることもしばしば。まだまだ初心者です。
無事完了⬇︎
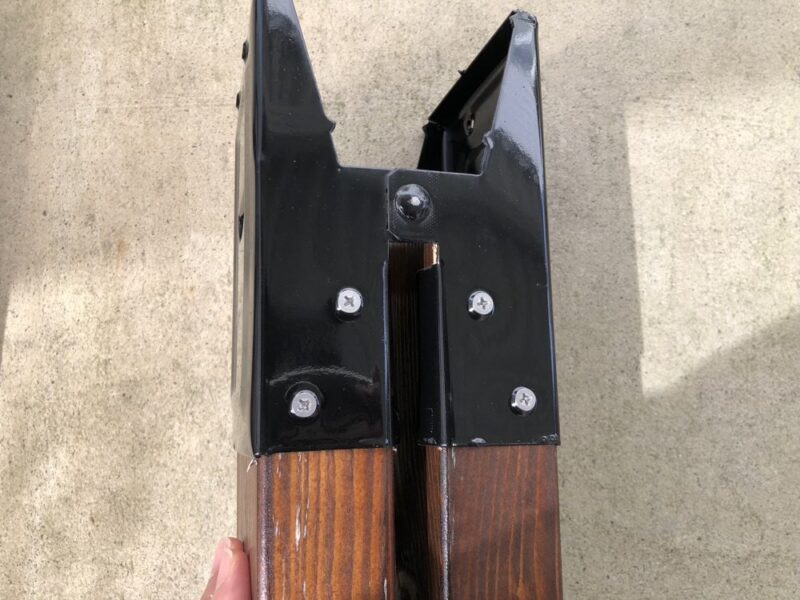
足を広げて棚受けを装着
棚受けを挟んでみました⬇︎
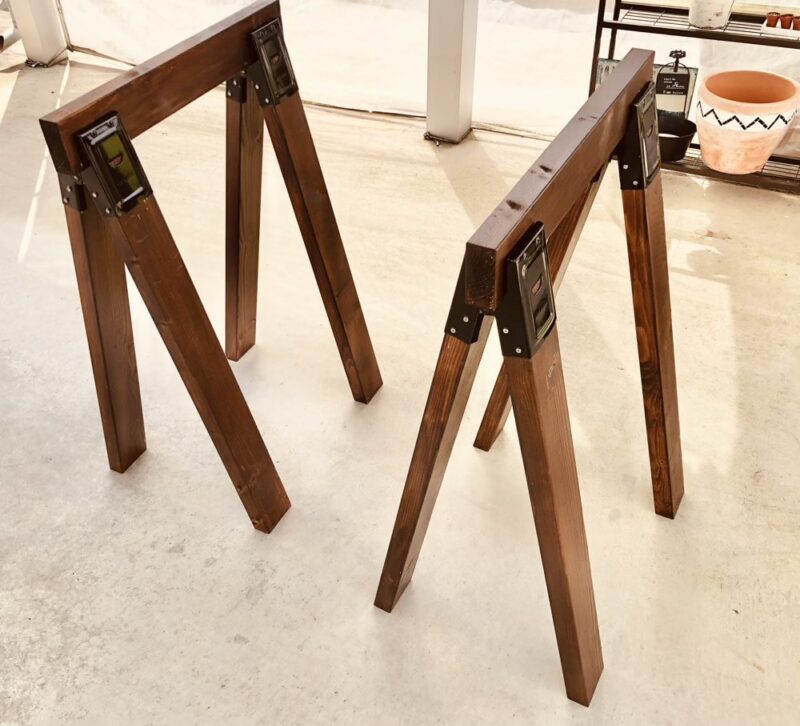
良い感じです!
ただ、ちょっと横にぐらつきますが、コンパクトに収納する事が目的なのでビス留めはしません。
取り外しできる固定方法
※固定しなくてもいい方は飛ばしても大丈夫です。
- 主な流れ
- ソーホースと棚受けに通し穴を加工
- M6サイズのボルトを通す
- ナットで締めて固定
ボルトの長さは80mmです。
貫通穴も4箇所だけにしました。
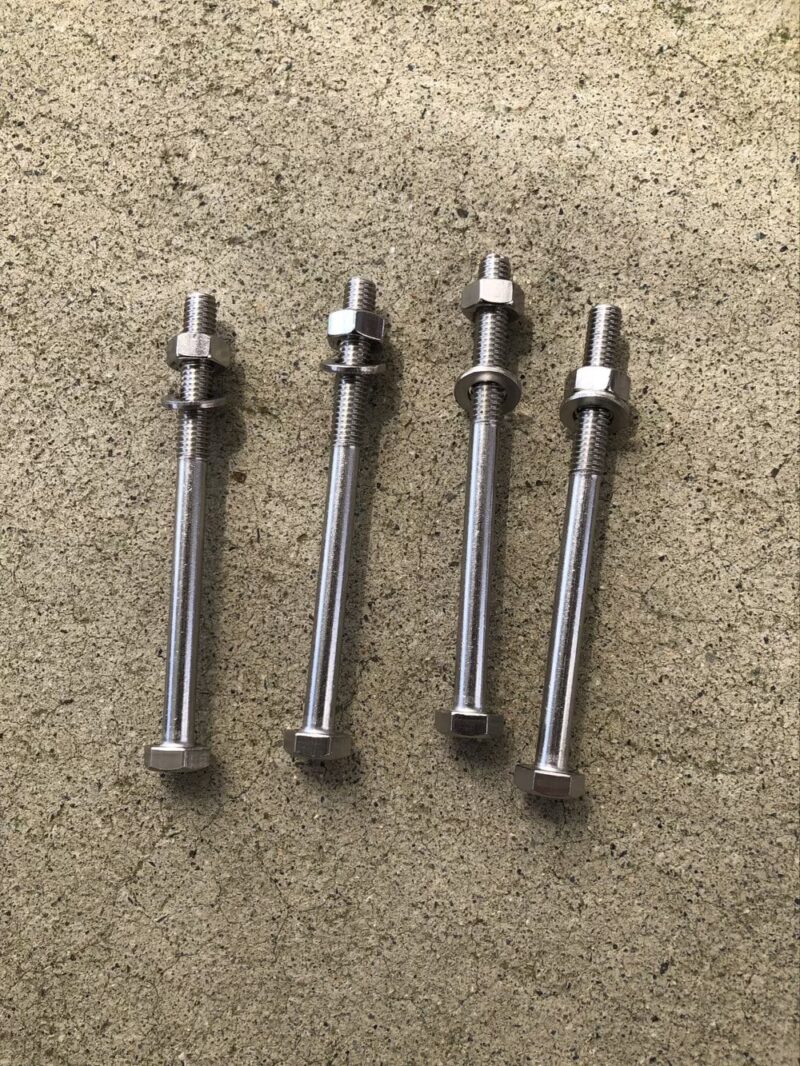
【ハプニング】貫通穴が小さすぎた
天板受け材にドリル直径6mmで貫通穴を加工。
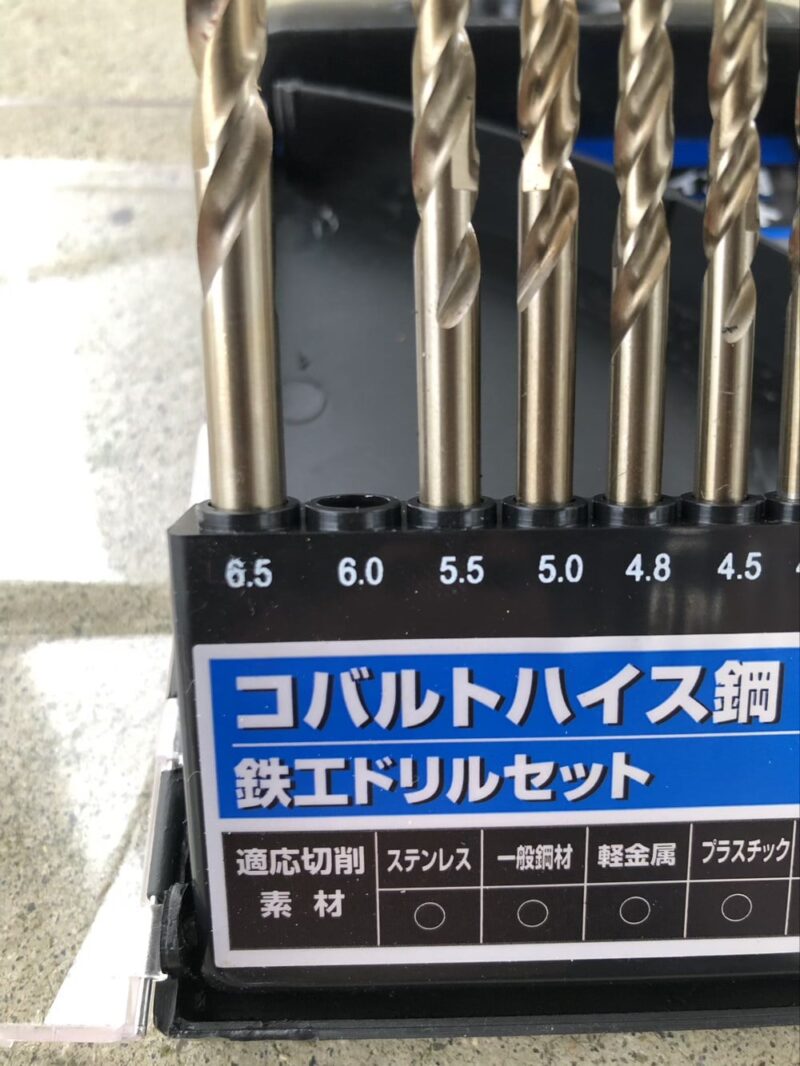
位置出し⬇︎
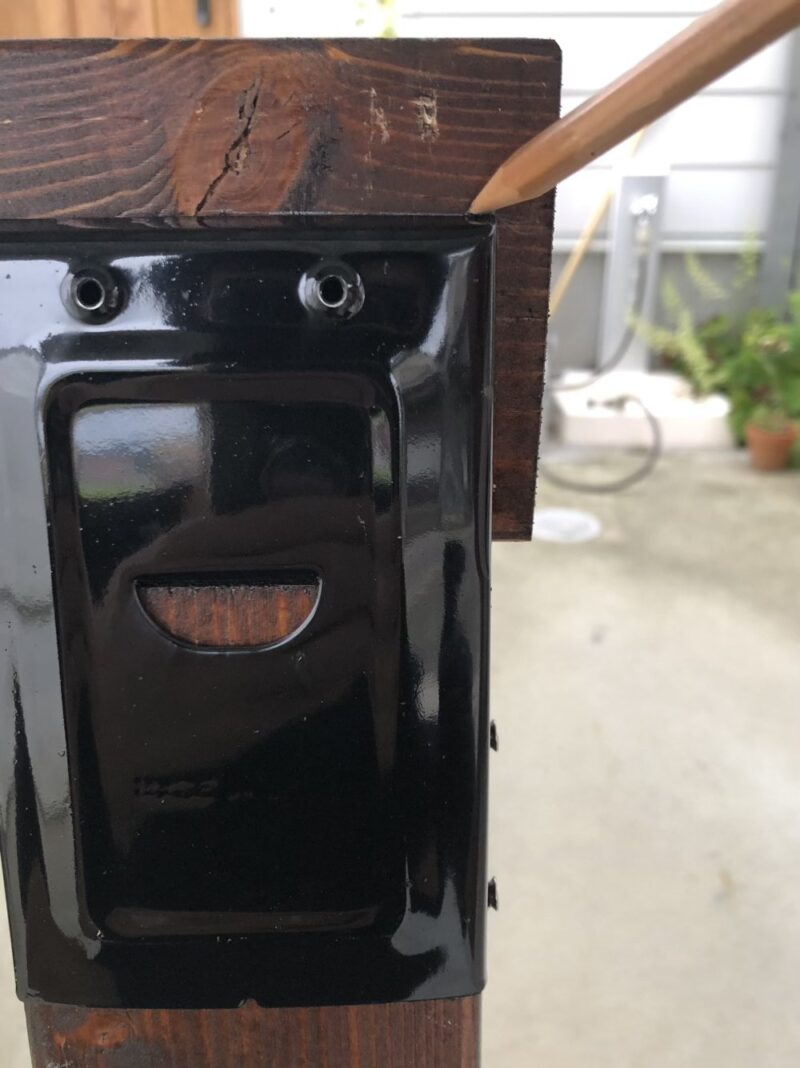
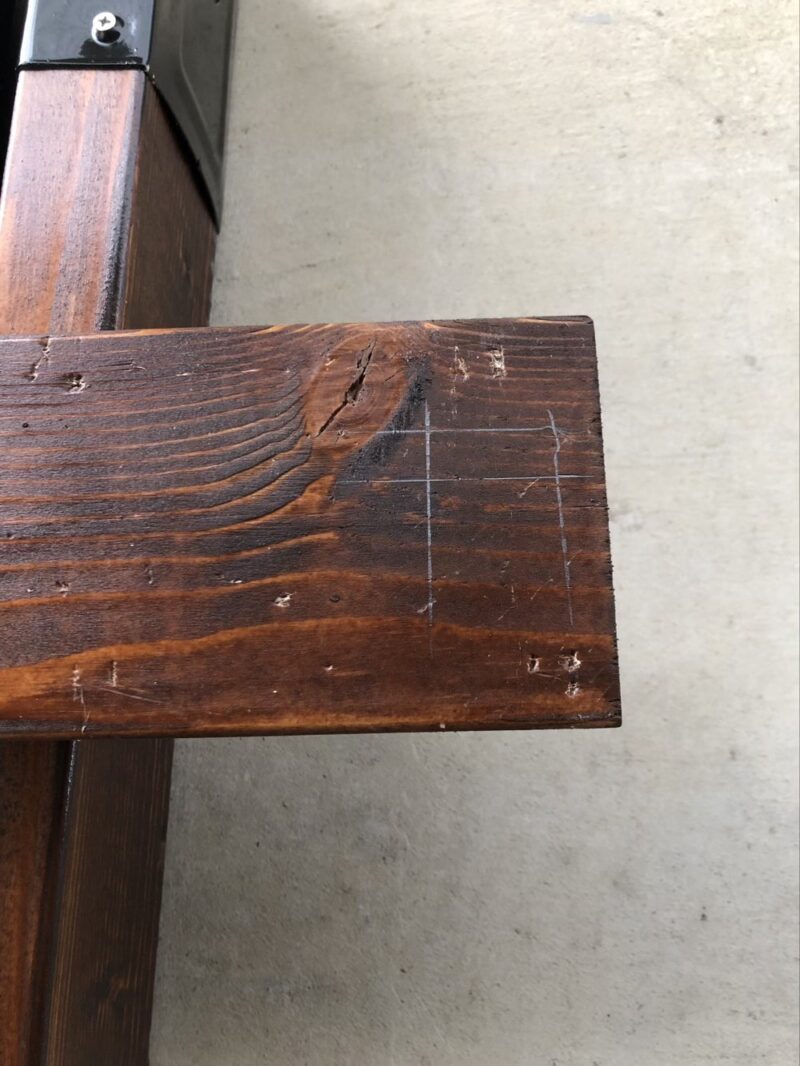
ソーホースのビス留め位置に印を付けます。
そして、ドリルガイドを使って真っ直ぐに加工します⬇︎
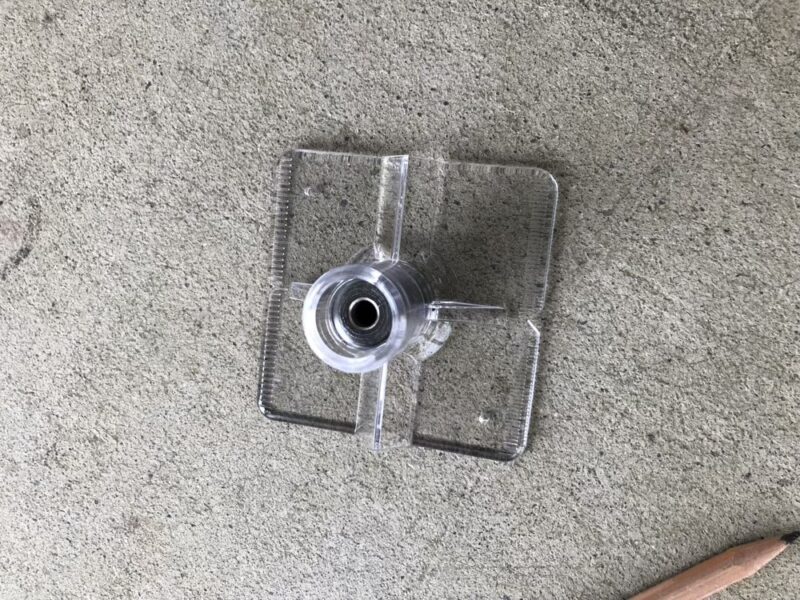
まずは付属品の針で加工位置に跡を付けます⬇︎ハンマーで叩いてます。
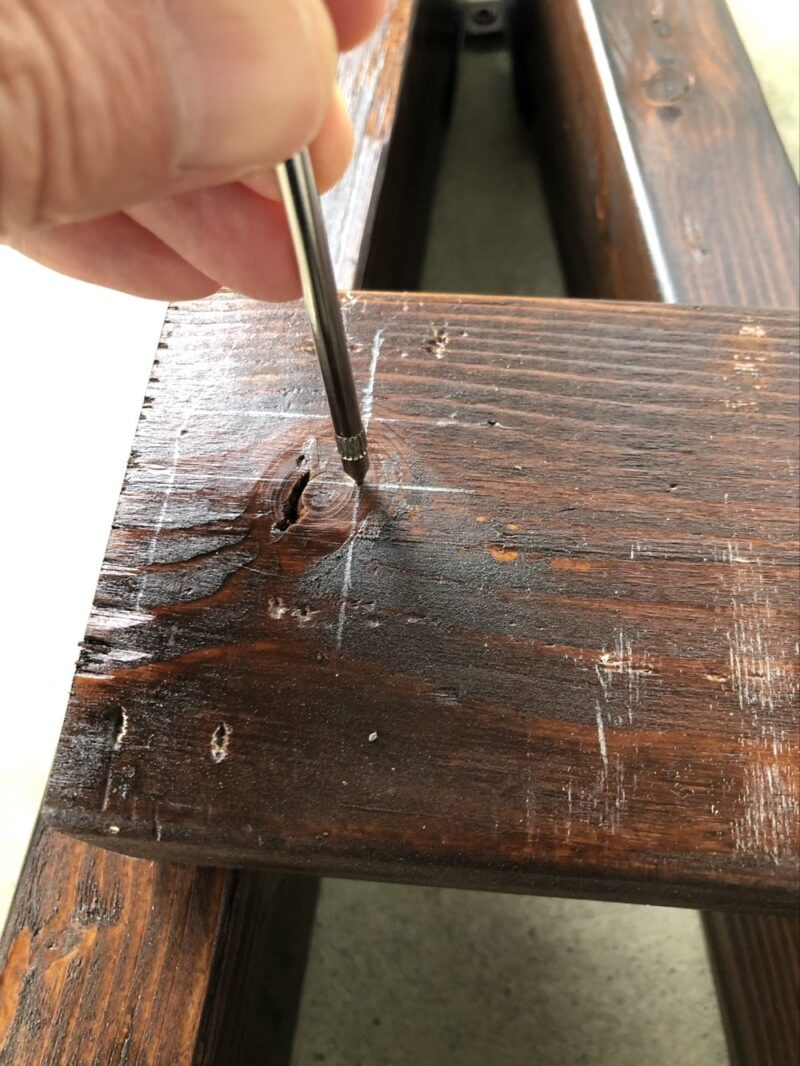
ドリルをガイドに入れて、ドリル先端を加工位置に合わせます。
合わせたら、ガイドがズレないようにハンドクランプなどで固定しておきました⬇︎
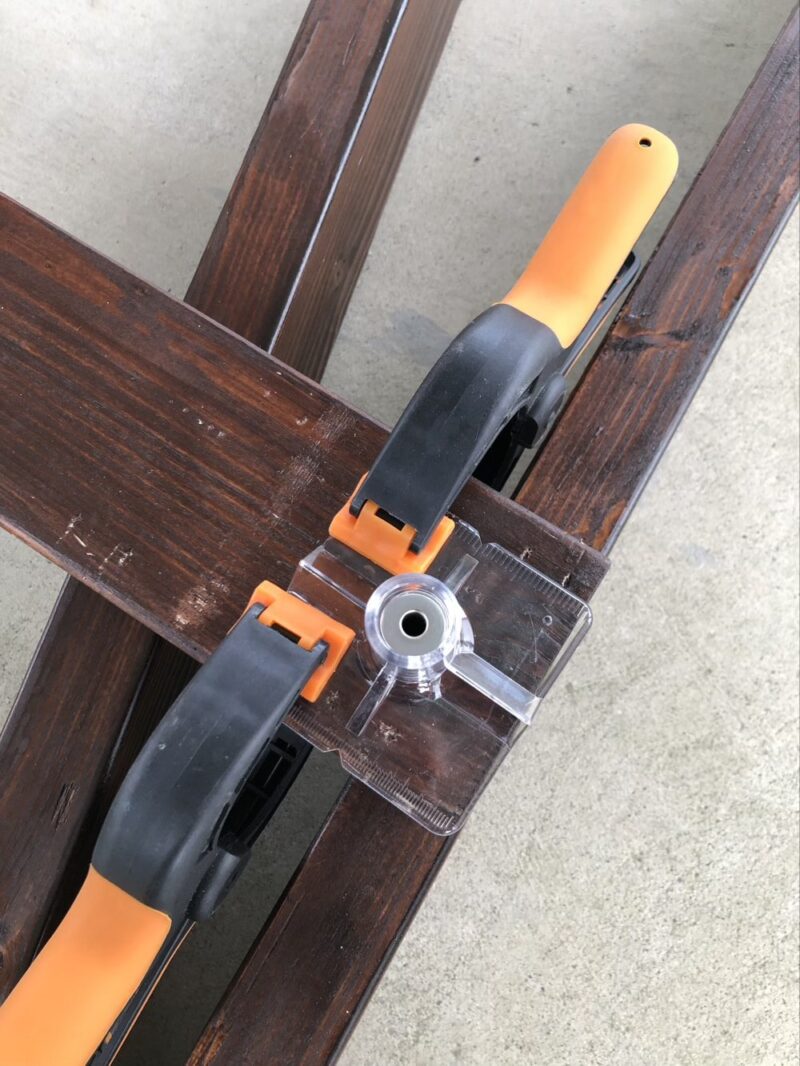
ドリル全長が短いため、両側から加工。合わせるのが難しいです。
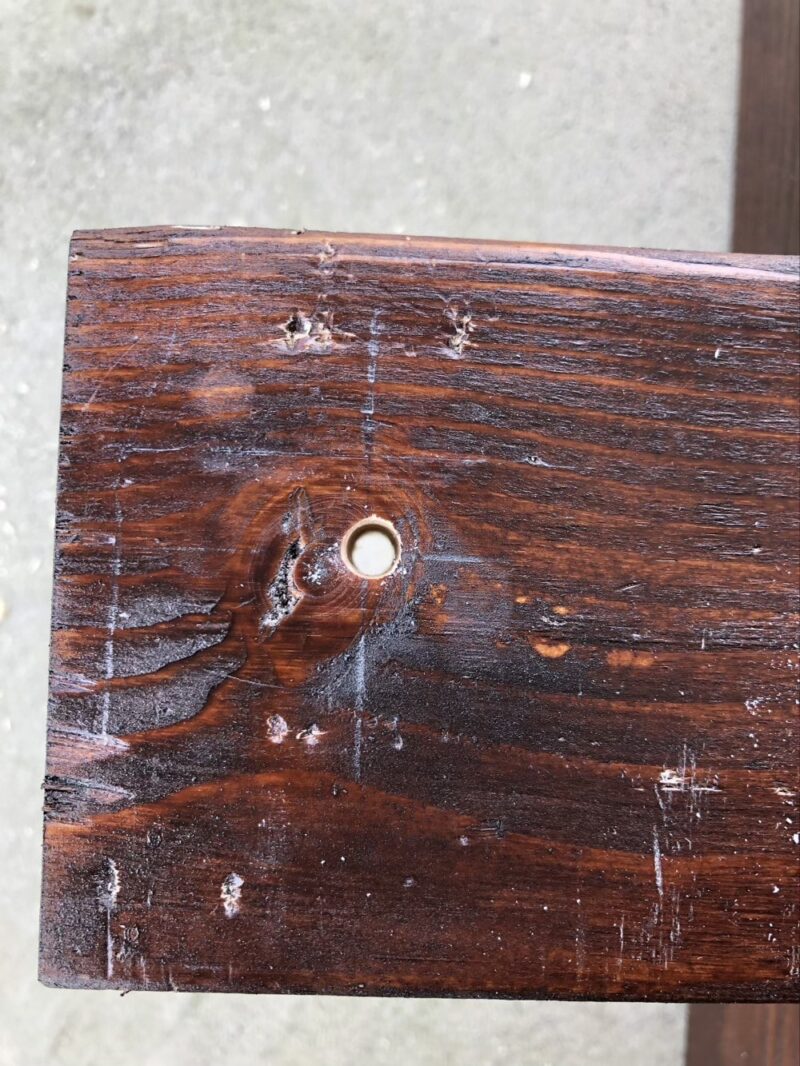
ドリルが長ければ一発でいけます。
しかし、直径6mmに対してM6ボルトはスムーズに入りません。

予想はしてたのですが、ドリルガイドにちょうどいいサイズが無くて。。。
【対策】ボルトを通し易くするために穴を広げる
φ6mm穴を6.5mmのドリルで広げます⬇︎
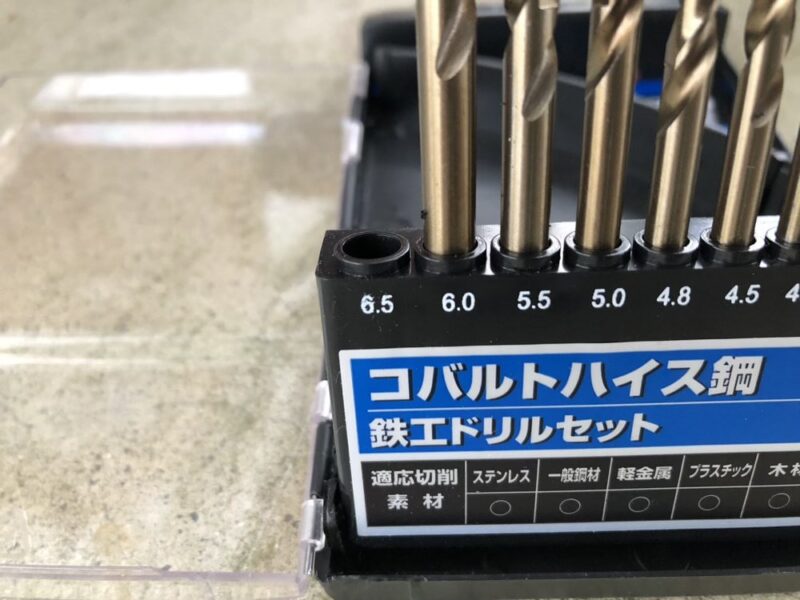
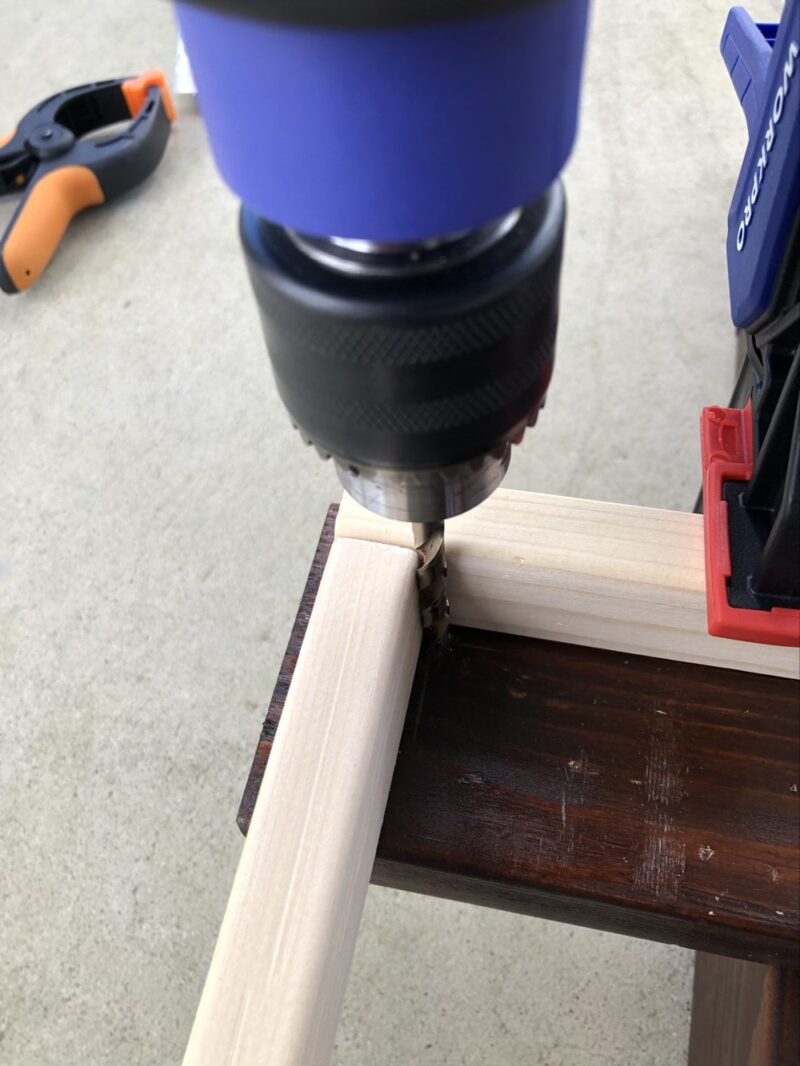
ドリルガイド替わりに自作の直角ガイドを使って真っ直ぐにドリル加工してます。
それでも上手に加工できません。
結局最後は直角ガイド無しで直接加工しました。
天板受けの4箇所に加工してます。
ソーホースにはいきなりドリル6.5mmで穴を広げました。
ボルトで固定して完成
ボルトを通してナットで締めれば完成です!
蝶ナットなら手締めできるので次の改善にしたいと思います。
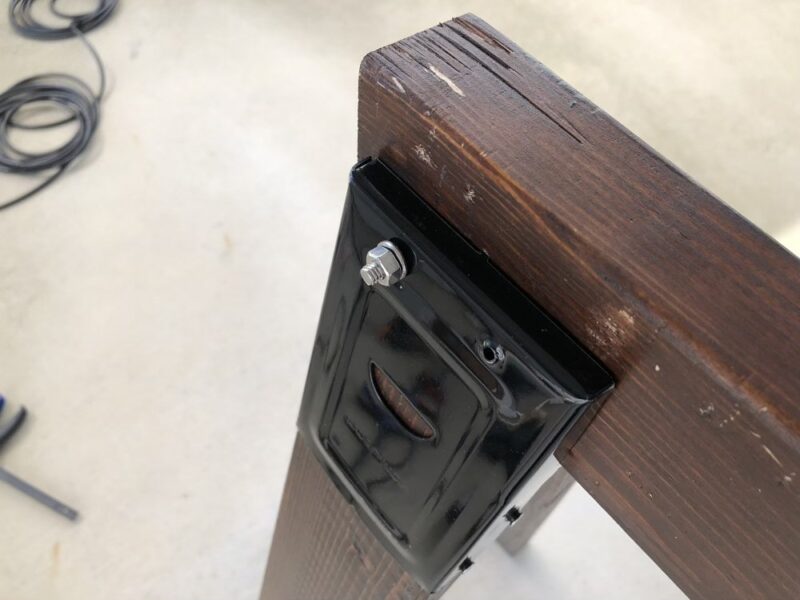
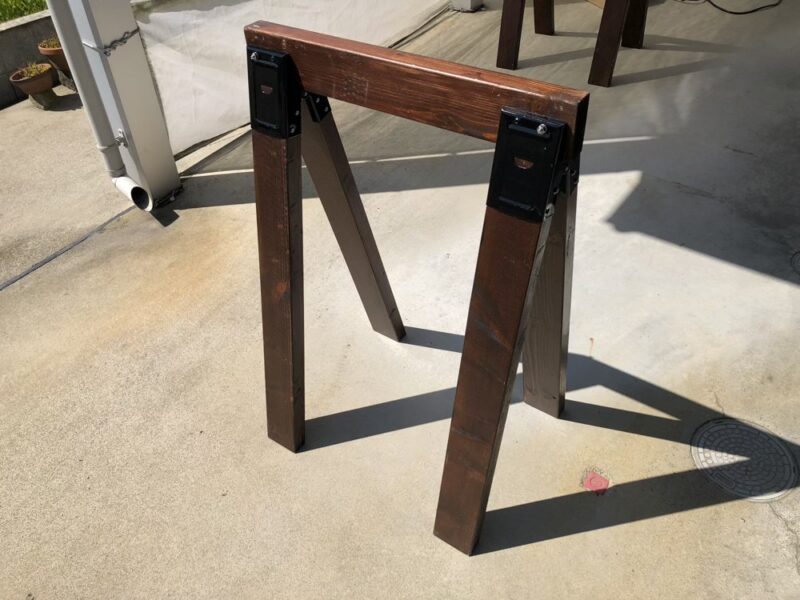
使わない時は分解して折りたたみ、カーポート天井裏棚に収納しています⬇︎
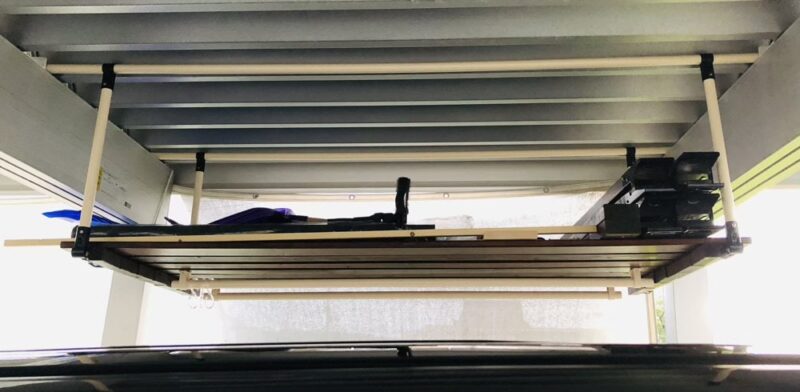
まとめ
- 主な材料は【ソーホース】【2×4材】【長さ80mmM6ボルト】
- 作業台高さ=(身長÷2)+5mm
- 木材の寸法を求める公式あります
- 木材足元は斜め13度で地面と平行
- 天板受けにM6ボルトが通る穴を加工して固定
- 使わない時は折りたたんで収納できる

これで腰をかがむコトなく作業ができるようになりました。